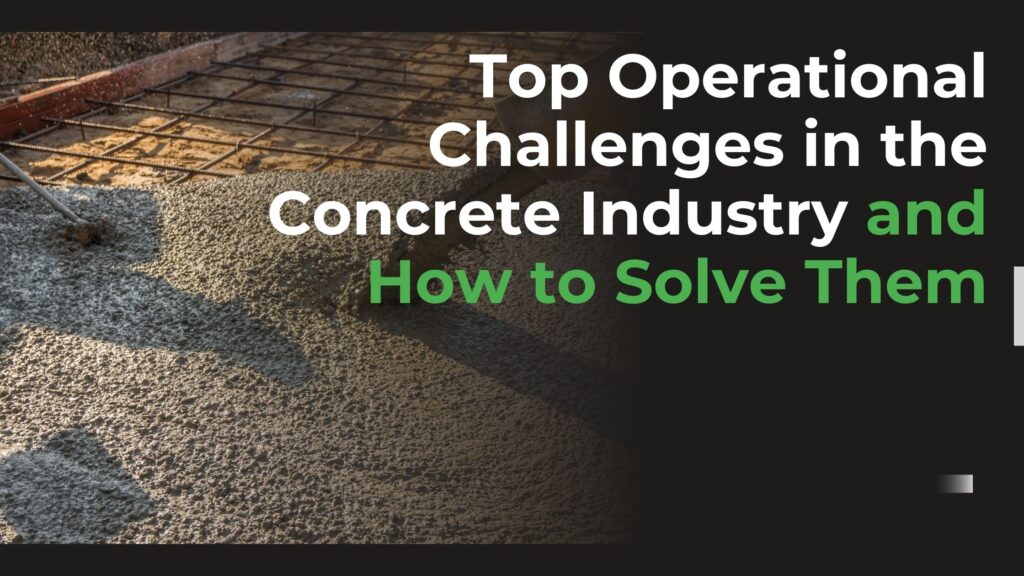
1. Challenge: Fragmented Systems
Concrete businesses often rely on separate systems for batching, fleet management, order processing, and invoicing. This fragmentation leads to inefficiencies, redundant data entry, and increased risks of errors.
Solution: Integrated Systems
Integrating these systems into a unified platform ensures seamless communication across operations. This eliminates the need for duplicate data entry and provides a real-time overview of your business, reducing errors and streamlining workflows.
2. Challenge: Inefficient Fleet Management
Timely deliveries are critical in the concrete business, but managing a fleet efficiently can be challenging. Issues like vehicle breakdowns, poor route planning, and delays can disrupt schedules and impact customer satisfaction.
Solution: Real-Time Fleet Tracking
Real-time fleet tracking systems enable businesses to monitor vehicle locations, optimise delivery routes, and improve scheduling. These tools provide insights that help reduce downtime, save fuel, and ensure on-time deliveries.
3. Challenge: Batching Inaccuracies
Accurate batching is essential to maintaining product quality and meeting customer specifications. Manual processes or poorly calibrated systems can result in costly mistakes, such as incorrect mix ratios.
Solution: Automated Batching Systems
Automated batching systems ensure precision by integrating recipe management and batch tracking. These systems minimise human error and maintain consistency, helping businesses meet quality standards and reduce waste.
4. Challenge: High Operational Costs
The concrete industry faces rising costs, from raw materials to labor and fuel expenses. Inefficiencies in operations can further drive up costs, eroding profit margins.
Solution: Process Optimisation
Streamlining operations through automation and integration reduces waste and saves time. Implementing systems that handle order processing, batching, and fleet management in one platform can significantly cut down on unnecessary expenses while improving overall efficiency.
5. Challenge: Limited Customer Visibility
Without clear communication and order tracking, customers can become frustrated with delays or lack of updates on their orders. This lack of transparency can damage customer relationships and lead to lost business.
Solution: Customer-Focused Tools
Online ordering platforms with tracking capabilities provide customers with real-time updates on their orders. These tools enhance transparency, improve customer satisfaction, and build stronger client relationships.
6. Challenge: Managing Multiple Job Sites
Coordinating operations across multiple job sites can be overwhelming, particularly when dealing with varying requirements, delivery schedules, and resource allocation.
Solution: Centralised Data Management
Integrated platforms consolidate information from all job sites into a single dashboard. This allows managers to monitor progress, allocate resources effectively, and ensure that each site runs smoothly without unnecessary delays.
7. Challenge: Environmental Compliance
The concrete industry faces increasing pressure to meet environmental regulations. Improper waste management or inefficient processes can lead to compliance issues and hefty fines.
Solution: Sustainable Practices
Adopting eco-friendly technologies and optimising production processes can help businesses meet regulatory requirements. Integrated systems also track environmental data, making it easier to monitor and improve compliance efforts.
8. Challenge: Labor Shortages
Finding skilled labor remains a challenge in the concrete industry, and high turnover rates can disrupt operations.
Solution: Upskilling and Automation
Invest in training programs to upskill your workforce and adopt automation to reduce dependency on manual labor. Automated systems for batching and fleet management not only alleviate labor shortages but also enhance productivity.
Conclusion
Operational challenges in the concrete industry don’t have to slow your business down. By implementing ICS, you can connect your existing systems—from online ordering and batching to fleet management and invoicing—into a unified platform. This reduces the need for repetitive data entry, minimises errors, and boosts efficiency across your entire operation. Ready to overcome these challenges? Discover how ICS can transform your business today.
Related Posts
The Benefits of Integrating Your Concrete Batching and Fleet Management Systems
Managing concrete batching and fleet operations can be a logistical nightmare without the right systems…
How Integrated Concrete Systems Simplifies Order Management
Order management is a cornerstone of any successful concrete business. But when your systems for…
How Leading Concrete Suppliers Are Streamlining Operations with ICS
The concrete industry relies on precise coordination between ordering, batching, and fleet management. Yet, many…