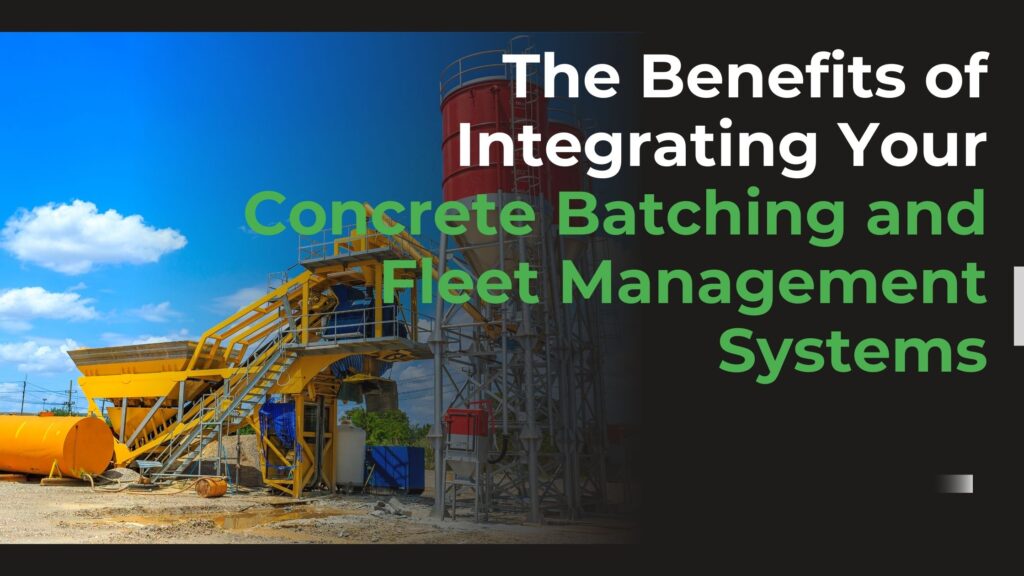
Managing concrete batching and fleet operations can be a logistical nightmare without the right systems in place. Many businesses rely on separate tools that don’t communicate effectively, resulting in inefficiencies, miscommunication, and expensive errors. Integrated Concrete Systems (ICS) bridges this gap by linking batching, fleet management, and other key operational components. With ICS, you get a streamlined workflow that enhances efficiency and accuracy, no matter which tools you already use.
1. Enhanced Operational Efficiency
Integrating batching and fleet management systems eliminates the need for manual coordination between production and delivery teams. When these systems communicate seamlessly, production schedules can align with fleet availability in real-time. This ensures that freshly batched concrete is delivered to the site promptly, reducing delays and minimising waste.
Key Benefits:
– Automatic scheduling and dispatching
– Reduced manual data entry and administrative tasks
– Faster decision-making through centralised dashboards
2. Improved Accuracy and Reduced Errors
Disjointed systems often result in miscommunication and data discrepancies, leading to costly mistakes such as incorrect batching recipes or missed delivery schedules. Integration ensures that data flows consistently between systems, reducing the likelihood of human errors and maintaining accuracy across operations.
Key Benefits:
– Consistent mix accuracy with automated batching
– Precise delivery schedules and reduced missed deadlines
– Fewer customer complaints due to improved reliability
3. Real-Time Monitoring and Insights
Integrated systems provide real-time visibility into production and logistics. Managers can monitor batching progress, track delivery vehicles, and address any issues as they arise. This proactive approach helps businesses stay ahead of potential delays and disruptions.
Key Benefits:
– Live tracking of vehicle locations and batching status
– Instant alerts for delays, equipment malfunctions, or traffic issues
– Enhanced ability to adjust schedules dynamically
4. Optimised Resource Utilisation
Without integration, businesses risk overproducing concrete or underutilising their fleet. Integrated systems optimise resource allocation by synchronising production with delivery capacity. This not only maximises fleet efficiency but also minimises material wastage.
Key Benefits:
– Better utilisation of delivery vehicles and batching equipment
– Reduced material wastage from overproduction
– Lower operational costs through efficient resource management
5. Streamlined Communication
Integration fosters seamless communication between teams. Drivers are provided with precise instructions, batching operators stay informed about delivery schedules, and managers can monitor the entire workflow seamlessly without managing multiple systems. This efficient communication guarantees that all team members are aligned and informed.
Key Benefits:
– Clear delivery instructions for drivers
– Real-time updates for batching and dispatch teams
– Improved collaboration and fewer misunderstandings
6. Increased Customer Satisfaction
Timely deliveries and consistent product quality are crucial to maintaining strong customer relationships. Integrated systems allow businesses to meet customer demands more effectively, providing accurate delivery times, consistent product quality, and better overall service.
Key Benefits:
– Reliable delivery schedules improve customer trust
– Consistent quality enhances customer satisfaction
– Transparent communication builds stronger client relationships
7. Comprehensive Reporting and Analytics
Integrated systems consolidate data from batching and fleet operations, offering valuable insights through detailed reports and analytics. Businesses can track performance metrics, identify inefficiencies, and make data-driven decisions to improve operations.
Key Benefits:
– Detailed reporting on delivery times, fleet performance, and production efficiency
– Insights into cost-saving opportunities
– Enhanced ability to plan for future growth and demands
Conclusion
Integrating your batching and fleet management systems doesn’t just save time—it transforms the way your business operates. ICS connects every element of your operations, from online orders and fleet schedules to batching and payments, ensuring that data flows seamlessly through every step of the process. Say goodbye to redundant tasks and costly mistakes, and let ICS help you achieve smoother, more efficient operations.
Related Posts
Top Operational Challenges in the Concrete Industry and How to Solve Them
The concrete industry faces numerous operational challenges, from managing fragmented systems to reducing costly errors.…
How Integrated Concrete Systems Simplifies Order Management
Order management is a cornerstone of any successful concrete business. But when your systems for…
How Leading Concrete Suppliers Are Streamlining Operations with ICS
The concrete industry relies on precise coordination between ordering, batching, and fleet management. Yet, many…