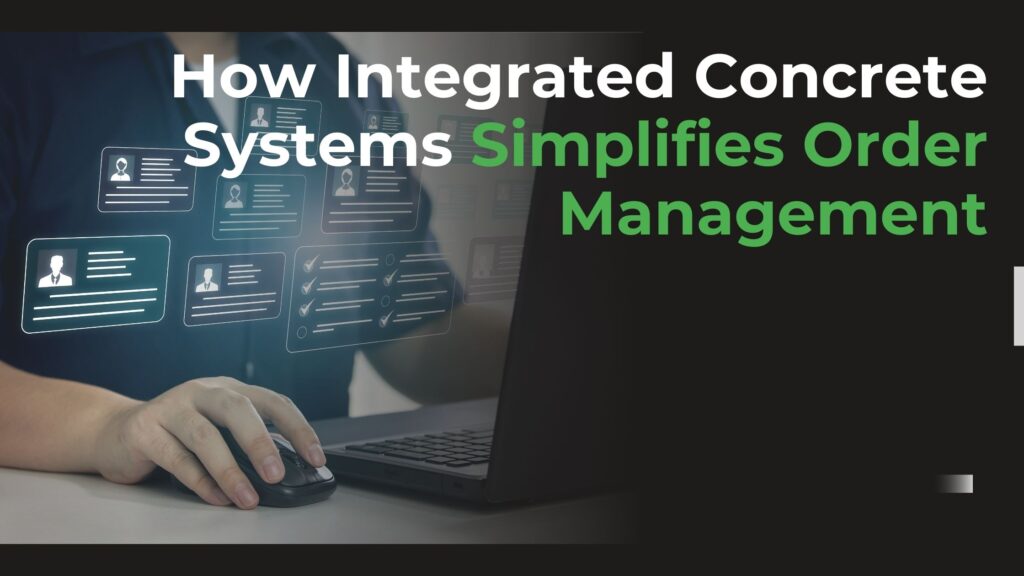
Order management is a cornerstone of any successful concrete business. But when your systems for batching, fleet planning, and invoicing operate in silos, managing orders becomes a time-consuming and error-prone task. Integrated Concrete Systems (ICS) solves this problem by linking all your operational tools into one cohesive system. This means orders are seamlessly processed from start to finish, reducing manual work and enhancing accuracy.
1. Centralised Order Management
One of the biggest challenges in the concrete business is managing multiple orders across different platforms. Integrated Concrete Systems bring all order-related activities—such as placing, modifying, and tracking orders—into a single platform. This eliminates the need to switch between systems and ensures that all information is up-to-date and easily accessible.
Benefits:
- One-stop dashboard for all orders
- Reduced risk of misplaced or forgotten orders
- Streamlined workflows for better productivity
2. Real-Time Updates and Visibility
Integrated systems provide real-time updates on order statuses, enabling businesses to monitor job progress at any given moment. Whether it’s batching, transportation, or delivery, all stages are tracked, providing complete visibility into the order lifecycle.
Benefits:
- Instant notifications for order changes or delays
- Improved planning and scheduling
- Enhanced decision-making with live data
3. Error Reduction with Automated Processes
Manual data entry often leads to errors, which can result in costly mistakes such as incorrect batching or delivery delays. Integrated systems automate order management tasks, reducing human error and ensuring accurate information flows through every stage of the process.
Benefits:
- Minimised data entry errors
- Consistent batching recipes for every order
- Greater reliability and fewer disruptions
4. Seamless Communication Between Teams
Integrated systems act as a bridge between different departments, ensuring that everyone involved in the order management process—batching operators, dispatch teams, and drivers—has access to the same information. This fosters better collaboration and ensures that changes are communicated promptly.
Benefits:
- Real-time communication between teams
- Reduced misunderstandings and delays
- Faster responses to client requests or changes
5. Customisable Order Options
Integrated systems allow businesses to offer tailored solutions to their customers. From choosing specific concrete mixes to scheduling deliveries, customers can customise their orders while the system ensures that these preferences are accurately captured and executed.
Benefits:
- Improved customer satisfaction with personalised options
- Simplified handling of complex orders
- Increased flexibility in meeting client demands
6. Enhanced Customer Experience
Customers value transparency and reliability. Integrated systems provide them with real-time updates on their orders, including delivery schedules and job progress. This not only boosts their confidence in your services but also enhances their overall experience.
Benefits:
- Transparency through order tracking
- Better communication with clients
- Strengthened customer relationships
7. Detailed Order History and Reporting
Integrated systems maintain a comprehensive record of all past orders, providing valuable insights for future planning and decision-making. With detailed reports, businesses can track trends, identify areas for improvement, and optimise their operations.
Benefits:
- Easy access to order history for audits or reviews
- Insights into customer preferences and demand patterns
- Data-driven strategies for operational efficiency
Conclusion
Simplifying order management is key to improving efficiency and customer satisfaction in the concrete industry. With ICS, your business benefits from a unified system that connects every aspect of order management—from customer orders to batching, fleet planning, and invoicing. This integration reduces errors, saves time, and ensures that every order is completed accurately and on time. Transform the way you manage orders with ICS and unlock new levels of productivity and reliability.
Related Posts
Top Operational Challenges in the Concrete Industry and How to Solve Them
The concrete industry faces numerous operational challenges, from managing fragmented systems to reducing costly errors.…
The Benefits of Integrating Your Concrete Batching and Fleet Management Systems
Managing concrete batching and fleet operations can be a logistical nightmare without the right systems…
How Leading Concrete Suppliers Are Streamlining Operations with ICS
The concrete industry relies on precise coordination between ordering, batching, and fleet management. Yet, many…